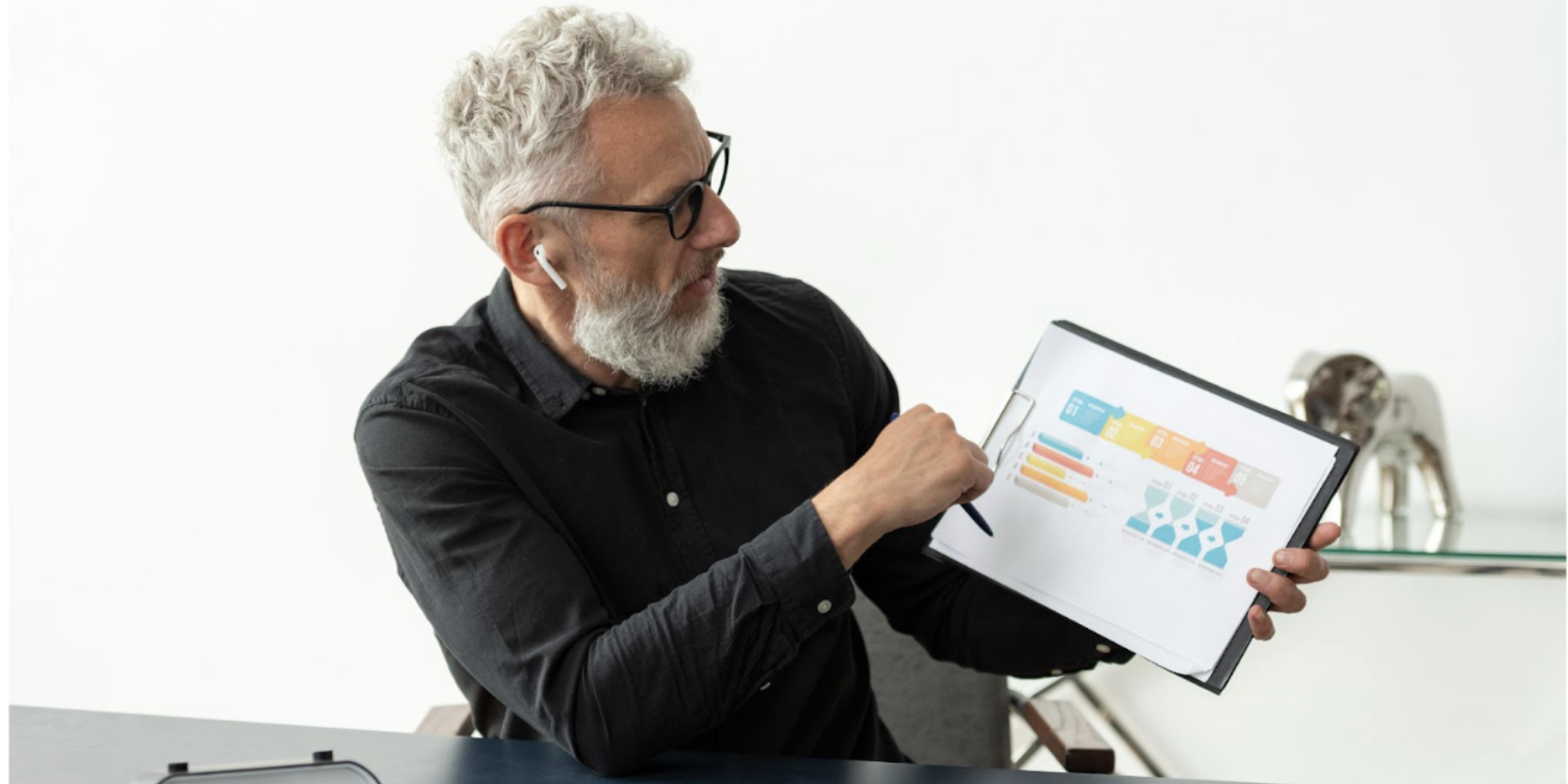
The ability to transform data into actionable insights has become a defining factor in manufacturing success. Manufacturing dashboards have emerged as indispensable tools, bridging the gap between raw data and strategic decision-making. Revolutionizing theme parks with digital signage demonstrates how real-time data can enhance visitor experiences—similarly, in manufacturing, dashboards provide a competitive edge by optimizing production efficiency and machine performance. These platforms consolidate real-time insights into production efficiency, machine performance, and quality metrics, providing manufacturers with the clarity needed to act swiftly and effectively.
By integrating data from multiple sources into one intuitive interface, manufacturing dashboards empower organizations to improve operational efficiency, minimize downtime, and enhance product quality. This article explores the vital role of manufacturing dashboards, their key features, and the challenges they address, offering a clear path to leveraging these tools for more tremendous success in the industrial sector.
Why are Manufacturing Dashboards Crucial?
Manufacturing dashboards provide a centralized platform for monitoring, analyzing, and optimizing operations. They simplify interpreting complex data sets by presenting key metrics in a user-friendly format. This real-time visibility enables organizations to identify inefficiencies, address production bottlenecks, and maintain consistent quality.
Dashboards also foster collaboration by offering a unified view of operational performance across departments. They support strategic planning through historical data analysis, enabling manufacturers to benchmark performance and set achievable goals. Beyond improving day-to-day operations, dashboards drive long-term growth by aligning decision-making with organizational objectives.
Real-Time Data Visualization Enhances Awareness
Real-time data visualization is a cornerstone of manufacturing dashboards, offering instant insights into operations. By tracking key performance indicators (KPIs) in real-time, manufacturers can monitor production efficiency, detect anomalies, and respond to issues as they arise. This level of awareness ensures a proactive approach to problem-solving, reducing delays and improving overall efficiency.
Quick Decision-Making Boosts Operational Responsiveness
Manufacturing dashboards streamline the decision-making process by consolidating data into actionable insights. With clear, up-to-the-minute metrics, managers can quickly and effectively respond to changes in demand, equipment performance, or supply chain disruptions. This rapid response capability reduces downtime and ensures operations run smoothly.
Operational Efficiency is Improved Through Data-Driven Insights
Dashboards enhance operational efficiency by analyzing both historical and real-time data. These insights enable manufacturers to optimize workflows, improve machine utilization, and minimize waste. Organizations can continuously refine processes based on dashboard feedback to achieve higher productivity and reduce resource consumption.
Types of Data Displayed on Dashboards
Manufacturing dashboards provide a comprehensive view of operations by displaying critical data in an organized and accessible format. Key data categories include production metrics, quality control indicators, maintenance records, and inventory levels. These metrics empower organizations to monitor performance, maintain quality standards, and manage resources effectively.
Production Metrics Include Output Rates and Cycle Times
Production metrics are essential for assessing the efficiency of manufacturing operations. Output rates reveal the volume of goods produced over time, while cycle times measure the duration of each production phase. Together, these metrics highlight areas for improvement and help optimize production workflows.
Quality Control Indicators such as Defect Rates
Defect rates are crucial quality control indicators that measure the percentage of products failing to meet standards. By monitoring these rates, manufacturers can pinpoint process weaknesses and implement corrective measures to improve product consistency and customer satisfaction.
Maintenance Records and Predictive Downtime Alerts
Maintenance records provide a detailed history of equipment performance, while predictive downtime alerts use data analytics to forecast potential failures. These features help organizations schedule preventive maintenance, reduce unexpected disruptions, and extend equipment lifespans.
Inventory Levels, Including Raw Materials and Finished Goods
Tracking inventory levels prevents shortages or overstocking and ensures a seamless production flow. Dashboards offer real-time visibility into raw materials and finished goods, helping manufacturers maintain optimal inventory levels and reduce storage costs.
Bridging Data and Action with Dashboards
Manufacturing dashboards act as the bridge between data collection and actionable insights. They transform raw data into a strategic asset by aggregating information from diverse sources. The intuitive visualization of KPIs enables quick decision-making, driving efficiency, quality, and resource allocation improvements.
Dashboards also facilitate continuous improvement by identifying trends and highlighting opportunities for process optimization. Integrating data into daily operations empowers organizations to stay competitive in a fast-paced industrial landscape.
Key Features of Effective Dashboards
The effectiveness of a manufacturing dashboard depends on its ability to adapt to user needs and integrate seamlessly with existing systems. Customizable interfaces, system integration, and mobile access are essential features that enhance usability and ensure dashboards remain a valuable tool for decision-makers.
Customizable Interfaces for Specific User Needs
A customizable interface allows users to tailor the dashboard to their specific roles and responsibilities. This flexibility ensures that each user has quick access to the metrics most relevant to their function, enhancing productivity and decision-making across all levels of the organization.
Seamless Integration with ERP and SCM Systems
Integration with enterprise resource planning (ERP) and supply chain management (SCM) systems enables dashboards to consolidate data across the organization. This unified view ensures consistency, improves data accuracy, and enhances the ability to make informed decisions based on a comprehensive operational overview.
Mobile Access for Decision-Making Anywhere, Anytime
Mobile access ensures that decision-makers can stay informed and responsive even when they are not on-site. Real-time updates delivered to mobile devices allow managers to address issues promptly, maintain operational continuity, and quickly adapt to changing circumstances.
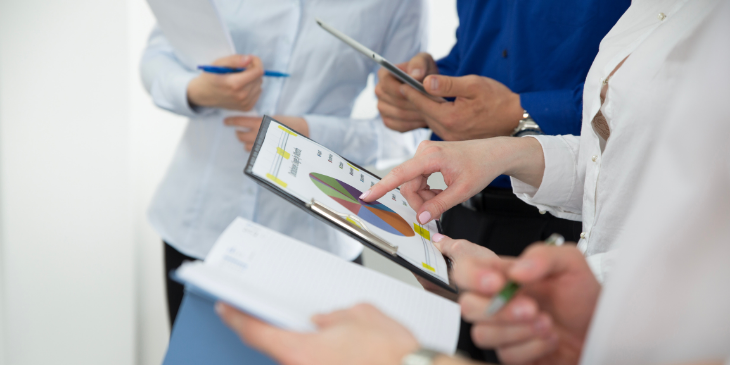
Implementing Dashboards Effectively
Implementing manufacturing dashboards requires a well-planned approach to ensure seamless integration and user adoption. This involves assessing data infrastructure, selecting relevant KPIs, and providing comprehensive training to maximize the dashboard’s utility.
Assessing Data Infrastructure for Readiness
Before deploying dashboards, it is essential to evaluate the existing data infrastructure. Systems must be capable of collecting, storing, and processing the high volumes of data generated by manufacturing operations. Ensuring a robust infrastructure is critical to the success of dashboard implementation.
Identifying KPIs Critical to Operational Success
Selecting the right KPIs ensures that dashboards provide actionable insights aligned with organizational goals. By focusing on metrics such as production efficiency, defect rates, and inventory levels, manufacturers can use dashboards to drive performance improvements and achieve measurable results.
Comprehensive Training for User Competency
Training programs are vital to ensure users can effectively navigate dashboards and interpret the data they display. Comprehensive training fosters confidence and competency, enabling employees to make informed decisions and fully leverage the dashboard’s capabilities.
Challenges in Dashboard Implementation
The implementation of dashboards can present challenges such as data silos, accuracy issues, and user adoption hurdles. Addressing these challenges is essential to ensure dashboards deliver meaningful insights and drive operational success.
Overcoming Data Silos for Unified Visibility
Data silos hinder the flow of information between departments, limiting the effectiveness of dashboards. Integrating disparate data sources into a cohesive system ensures a unified view of operations, enhancing collaboration and decision-making.
Ensuring Data Accuracy for Reliable Decision-Making
Accurate and up-to-date data is the foundation of effective dashboards. Establishing robust data validation processes ensures that decisions based on dashboard insights are reliable and beneficial to operational outcomes.
Facilitating User Adoption Through Change Management
Encouraging user adoption requires a focus on change management, including clear communication of the dashboard’s benefits and ongoing support. Engaging employees in the implementation process fosters a culture of data-driven decision-making and ensures long-term success.
Dashboards and Industry 4.0 Evolution
Manufacturing dashboards are key to the evolution of Industry 4.0. Integrating with IoT devices and advanced analytics provides real-time insights into every aspect of production. Dashboards enable predictive maintenance, optimize workflows, and support the seamless interaction between humans and digital systems.
As a cornerstone of Industry 4.0, dashboards empower manufacturers to achieve greater efficiency, agility, and innovation. They transform data into a competitive advantage, ensuring organizations stay ahead in a rapidly changing industrial landscape.
Why Choose Rise Vision for Manufacturing Dashboards?
Rise Vision is a leader in providing digital signage and dashboard solutions tailored to manufacturers' unique needs. Their platforms enable real-time data visualization, seamless integration with existing systems, and customizable features that align with operational goals. Whether you aim to optimize workflows, improve safety, or enhance decision-making, Rise Vision’s innovative tools can help you succeed.
Rise Vision is committed to delivering user-friendly, scalable, and free cloud-based digital solutions. It empowers businesses to turn data into actionable insights that drive growth. Ready to elevate your manufacturing operations? Explore the power of Rise Vision dashboards today.