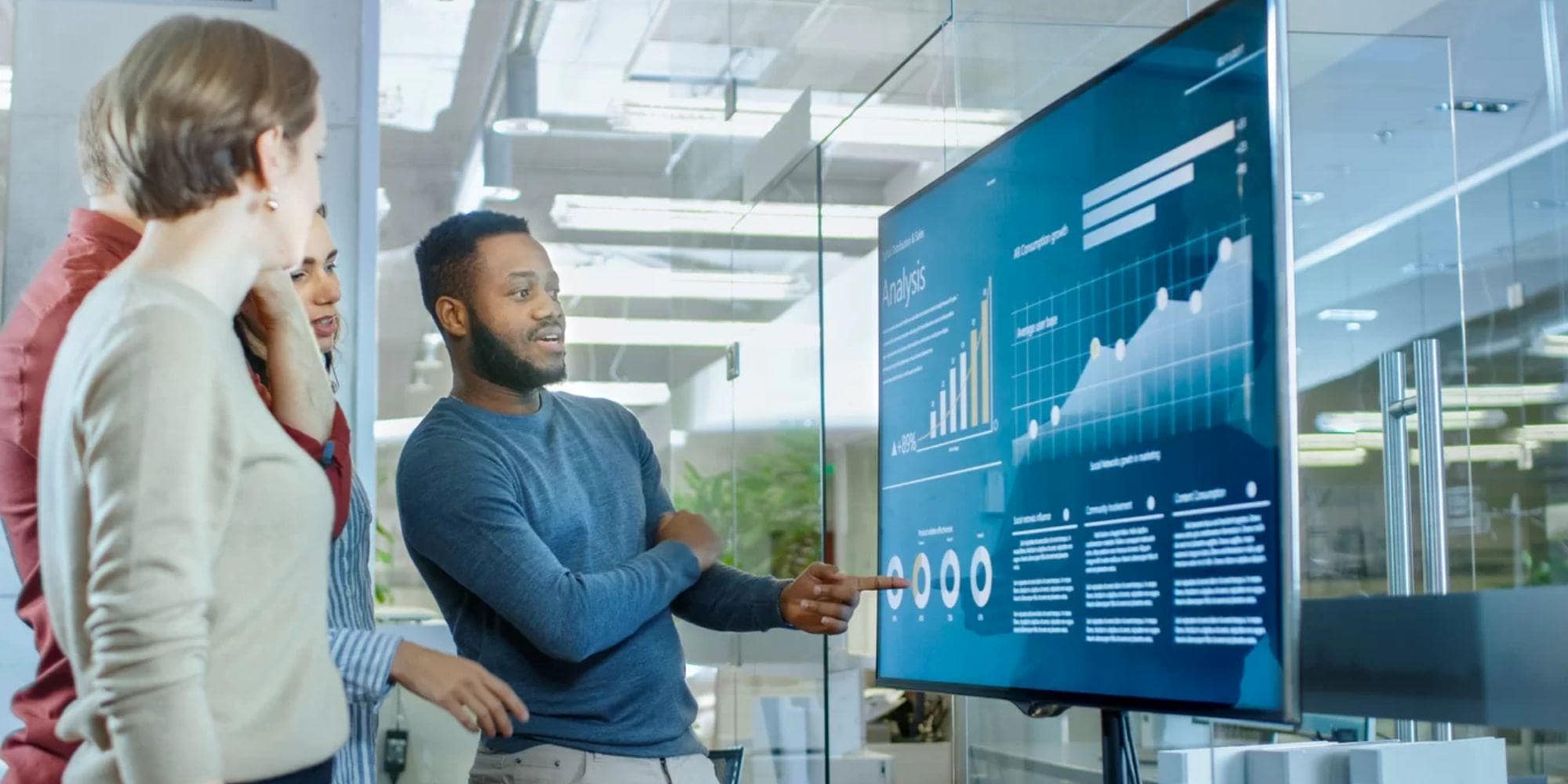
Maintaining high-quality standards is vital for sustained success in the manufacturing sector. Digital signage has emerged as a potent tool for enhancing quality management within manufacturing enterprises. Seamlessly integrating digital displays into your quality control system opens up avenues for real-time monitoring, data visualization, and process optimization. For more insights into how digital signage is revolutionizing the manufacturing sector, explore our comprehensive guide on digital signage in industrial setting.
The impact of manufacturing digital signage on quality management can be transformative, reshaping how businesses ensure product integrity and compliance. However, realizing these benefits hinges on strategic implementation and effective utilization.
How Digital Signage Benefits Manufacturing
Digital signage software in manufacturing facilities significantly enhances operational efficiency and communication by providing real-time data visualization and targeted messaging. Displaying key performance indicators (KPIs) throughout the facility enables employees to track production metrics easily and identify areas for improvement. Moreover, digital signage is a conduit for communicating critical updates, safety protocols, and company announcements in real time, ensuring staff members remain informed and aligned. This technology streamlines information dissemination, reducing reliance on outdated methods like printed materials or email communications. Research by MarketsandMarkets indicates that the adoption of digital signage for quality management is projected to grow at a CAGR of 7.9% from 2021 to 2026. Consequently, integrating digital signage leads to improved productivity, enhanced communication, and a more efficient operational environment. According to TelcoNews, 86% of businesses reported improved communication and productivity by implementing digital signage in quality management processes.
20 Best Practices for Implementing Digital Signage in Quality Control
Successful implementation of digital signage in quality control requires clear objectives and goals. Understanding audience needs, selecting suitable hardware and software, creating relevant content, and ensuring visibility and accessibility are critical steps for effective utilization. By adhering to these best practices, companies can enhance their quality control processes and optimize overall quality management through digital signage.
Define Objectives and Goals
In quality management, setting clear and measurable objectives and goals is crucial for the successful integration of digital signage in quality control practices. To define objectives and goals effectively for your digital signage system, adhere to the following best practices:
- Identify Key Performance Indicators (KPIs): Determine the specific metrics targeted for improvement through digital signage.
- Establish Realistic Targets: Set achievable goals that align with overarching quality control objectives.
- Ensure Relevance: Verify that the objectives are pertinent to enhancing quality control processes.
- Monitor Progress: Implement a tracking system to monitor and assess progress toward achieving the established goals.
- Regularly Review and Adjust: Continuously evaluate the efficacy of the objectives and make necessary adjustments to optimize quality control practices.
Understand Audience Needs
Understanding the specific needs and preferences of the target audience is essential when implementing digital signage in quality control practices to ensure effective communication and engagement. Thorough audience analysis, including demographics, organizational roles, and preferred communication styles, allows businesses to tailor their digital signage content to resonate with employees involved in quality control processes.
This customization can increase attention and comprehension of quality management information, ultimately enhancing overall quality control procedures. Additionally, considering the varying levels of technical expertise among employees can aid in designing user-friendly interfaces and content that cater to a diverse audience, ensuring maximum effectiveness of the digital signage system in quality control.
Choose the Right Hardware and Software
Selecting the appropriate hardware and software is crucial for successfully implementing digital signage in quality control. When choosing hardware and software for your manufacturing business, prioritize the following factors:
- Compatibility: Ensure compatibility with existing systems to facilitate seamless integration.
- Scalability: Opt for solutions that can grow alongside your business to accommodate future needs.
- Reliability: Choose reliable hardware and software to minimize downtime and ensure continuous operation.
- User-Friendly Interface: Prioritize intuitive interfaces that are easy for employees to navigate and use effectively.
- Remote Management: Look for options that offer remote monitoring and management capabilities for enhanced convenience and efficiency.
By carefully considering these factors, you can establish an effective digital signage system for quality control in your manufacturing business.
Create Clear and Relevant Content
To ensure the effective use of digital signage in quality control, it's important to create personalized content that is clear, relevant, and engaging for both employees and stakeholders.
Focus on displaying key quality metrics, real-time production data, quality standards, and any pertinent updates or announcements. Utilize visual aids like graphs, charts, and images for quick and effective communication. Keep the messaging concise, easy to understand, and aligned with your quality management system goals. Regularly update the content to maintain freshness and relevance, avoiding unnecessary clutter.
By crafting clear and relevant content, you can enhance communication, facilitate better decision-making, and drive overall quality improvement in your manufacturing business.
Ensure Visibility and Accessibility
Another important factor for effective communication and transparency within the manufacturing environment is ensuring that digital signage in quality control is visible and accessible. To achieve this, follow these best practices:
- Position digital signage at key locations where quality control activities occur.
- Ensure signage is large enough to be easily read from a distance.
- Use legible fonts and contrasting colors to improve readability.
- Display only essential information to prevent overload.
- Conduct routine checks to ensure signage functions correctly and content remains up to date.
Provide Real-Time Data Updates
By incorporating real-time data feeds into the signage system, manufacturing businesses can offer immediate updates on vital quality metrics, production status, and any emerging quality issues. This empowers employees to promptly make informed decisions, resulting in enhanced quality control processes and better problem resolution. Moreover, real-time data updates contribute to fostering transparency and accountability within the organization. Stakeholders gain access to timely quality data, promoting a culture of continuous improvement and excellence in quality.
Standardize Content Templates
With the help of standardized content templates, businesses can ensure a uniform display of critical information across all screens, facilitating streamlined communication and decision-making. The following best practices underscore the significance of standardizing content templates:
- Consistent Messaging: Ensuring accurate conveyance of information across all displays.
- Brand Cohesion: Maintaining a consistent look and feel across signage to strengthen brand identity.
- Ease of Updates: Simplifying content updates across multiple screens.
- Compliance Requirements: Meeting industry standards and regulations with standardized templates.
- Enhanced Visibility: Improving content visibility and readability for all stakeholders.
Display Key Performance Indicators (KPIs)
Utilizing digital signage to showcase Key Performance Indicators (KPIs) is a strategic approach that enhances real-time monitoring and decision-making processes in quality control management for manufacturing businesses.
By displaying KPIs such as production efficiency, defect rates, and on-time delivery metrics on digital screens in prominent areas of the manufacturing facility, employees at all levels can access crucial performance data instantly. This visibility cultivates a culture of transparency, accountability, and continuous improvement within the organization. Additionally, digital KPI displays facilitate rapid identification of bottlenecks or areas requiring attention, enabling swift corrective actions.
Overall, leveraging digital signage for KPIs empowers manufacturing businesses to effectively drive operational excellence and uphold quality standards.
Encourage Visual Management Techniques
Visual management techniques contribute to process optimization, better communication, and increased efficiency. Consider these five strategies to implement:
- Employ color-coded displays to signify various production stages.
- Integrate digital dashboards for live updates on quality metrics.
- Utilize visual cues like charts, graphs, and images for swift comprehension of complex information.
- Showcase standardized work instructions and quality control procedures on digital screens.
- Enhance engagement and participation by integrating interactive elements such as touchscreens.
Highlight Safety Protocols and Procedures
By prominently displaying safety protocols and procedures through digital signage, manufacturing businesses can continuously remind employees of best practices and potential hazards. This visual reinforcement plays a crucial role in accident prevention, error reduction, and the promotion of a safety-oriented workplace culture.
Clear and concise messages on digital screens effectively capture attention and offer real-time updates on safety guidelines, emergency procedures, and other critical information. Integrating safety messages into the daily workflow through digital signage significantly enhances the safety and efficiency of the quality control environment.
Integrate with Quality Management Systems (QMS)
Integrating digital signage with Quality Management Systems (QMS) is a critical step in enhancing quality control practices within manufacturing businesses. This integration allows companies to streamline quality control processes, improve communication, and ensure compliance with industry standards. Here are five key benefits of integrating digital signage with QMS:
- Facilitates real-time monitoring of quality performance.
- Provides automated alerts for quality deviations.
- Offers a centralized display of quality Key Performance Indicators (KPIs).
- Enhances visibility of quality objectives.
- Enables seamless integration with quality audit processes.
This integration empowers manufacturing businesses to proactively manage quality control, drive continuous improvement, and ultimately deliver products that meet or exceed customer expectations.
Highlight Quality Cost Savings Initiatives
Implementing digital signage in quality control processes can yield significant cost savings through efficient communication of quality initiatives and performance metrics. Employees are constantly reminded of the importance of cost-effective quality practices by highlighting quality cost savings initiatives on digital displays throughout the manufacturing facility.
Displaying real-time data on defect rates, rework costs, and other quality metrics can help identify areas for improvement and encourage proactive problem-solving. This transparency fosters a culture of continuous improvement and cost consciousness among employees.
Furthermore, by showcasing successful cost-saving initiatives and their impact on the bottom line, digital signage can motivate teams to actively seek out innovative ways to reduce quality costs and streamline processes, leading to tangible financial benefits for the manufacturing business.
Provide Training and Tutorials
By providing employees with comprehensive training and tutorials on utilizing digital signage in quality control processes, organizations can effectively enhance understanding and implementation of best practices for optimizing quality management systems. This includes developing interactive training modules that simulate real-world quality control scenarios, offering hands-on workshops for practicing the use of digital signage tools, providing refresher courses to reinforce key concepts and address challenges, and creating user-friendly manuals and guides for easy reference. Additionally, encouraging feedback from employees enables continuous improvement of training materials and methods.
Through these strategies, companies can empower their workforce to effectively leverage digital signage for quality control processes.
Celebrate Achievements and Milestones
In cultivating a culture of excellence within quality control processes, digital signage emerges as a potent tool for motivating employees. By highlighting successful projects or milestones, you inspire pride and motivation. Recognizing hard work publicly through digital displays reinforces the importance of quality standards and encourages ongoing efforts for improvement. This celebration fosters a positive work environment that values success.
Using digital signs for this purpose improves communication and engagement within the department and company-wide.
Solicit Employee Feedback and Suggestions
Incorporating digital signage to solicit employee feedback and suggestions in quality control processes can significantly enhance workforce engagement and continuous improvement efforts. By leveraging digital displays strategically, businesses can create a platform for open communication and collaboration within the organization. Here are some best practices for implementing digital signage to solicit employee feedback and suggestions:
- Encourage anonymous submissions to ensure honest feedback
- Provide prompts or questions to guide employees in their suggestions
- Display feedback in real-time to show employees their input is valued
- Implement a system to track and address suggestions effectively
- Use visual aids such as graphs or charts to highlight trends in feedback
Schedule Content Rotation
Scheduled content rotation at manufacturing can keep employees engaged and informed about quality control procedures, updates, and best practices. A well-planned rotation strategy can prevent information overload and ensure critical messages are consistently displayed for optimal visibility. It also allows for regularly updating content to reflect any changes in processes or quality standards. Moreover, a scheduled rotation helps maintain employee interest and attention toward digital signage, enhancing its effectiveness in communicating important quality management information throughout the manufacturing facility.
Facilitate Problem-solving Sessions
Conducting problem-solving sessions with digital signage can greatly improve its utilization in quality control. Encourage active participation from all team members to promote collaboration and innovative solutions. Utilize real-time data and quality metrics displayed on the signage to identify issues effectively. Foster open communication and a culture of continuous improvement by using interactive features to gather input and feedback. Additionally, visual aids and diagrams should be implemented to facilitate problem analysis and enhance understanding among employees.
Ensure Security and Data Privacy
Ensuring security and data privacy is crucial when implementing digital signage in quality control. Robust measures such as secure network connections and encrypted data transmission are essential to safeguard sensitive information. Regular software updates and security audits help mitigate risks of unauthorized access or data breaches. Compliance with industry regulations such as GDPR or HIPAA should also be prioritized.
By proactively addressing security concerns, manufacturing businesses can maintain operational excellence while protecting valuable data from potential threats.
Monitor Display Performance and Health
Monitoring display performance, and health is crucial for maintaining effective digital signage in quality control.
Regular checks for physical damage or defects, along with software tools to track performance metrics like brightness and resolution, ensure optimal functionality. Scheduled maintenance and cleaning prevent issues, while alerts for anomalies enable prompt action. Calibration ensures consistent output.
By systematically monitoring display health, businesses can uphold quality control standards, minimize disruptions, and sustain the reliability of their digital signage systems, thus supporting overall operational efficiency and effectiveness.
Iterate and Improve
Regularly reviewing the content displayed on digital signage screens within the manufacturing facility can help identify areas for enhancement. Soliciting feedback from employees involved in quality control processes can provide valuable insights into what information should be prioritized on the displays. Furthermore, analyzing the impact of digital signage on quality control metrics, such as defect rates or production efficiency, can guide adjustments to the content or placement of screens.
Key Takeaways
When considering quality management through digital signage, keep in mind the following key takeaways:
- Real-time Monitoring: Utilize free digital signage to monitor quality metrics in real time.
- Instant Notifications: Receive immediate notifications for any deviations from quality standards.
- Data Visualization: Use digital signage to represent quality data for easy visual analysis visually.
- Continuous Improvement: Implement a cycle of continuous improvement based on insights gathered from digital signage data.
- Employee Engagement: Engage employees by displaying quality goals, achievements, and areas for improvement on digital signage screens.